How to correctly install the inlet and outlet pipes of the fan coil unit and avoid water leakage?
Featured articles
The installation quality of cooling tower piping directly impacts operational safety. 37% of air conditioner leakage failures are caused by improper installation. Applying scientific installation procedures can effectively prevent ceiling leaks, equipment damage, and other malfunctions. The following core tutorial examines detailed leak-proof considerations.
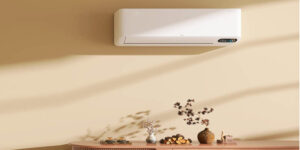
Material Selection: Building Leak-Proof Foundations
Hot water systems should utilize hot-dip galvanized steel pipes (DN≤100mm) or PP-R pipes (temperature tolerance ≤70℃). Cold water systems may use galvanized steel pipes or PE-RT pipes. Employ 45° or 90° elbow press fittings with curvature radius ≥1.5D. Bronze valves must have pressure ratings ≥1.6MPa, with EPDM seals for hot water and NBR for cold water.
For steel pipe connections:
- Wrap PTFE tape clockwise (5-7 layers)
- Apply thread sealant
PP-R hot fusion temperature: 260±10℃. Welding duration: 6 seconds for DN25 pipes. Install rubber flexible joints (working pressure ≥1.0MPa) 150-300mm from coil connections. Terminate with fixed supports.
Standard Installation: Core Leak Prevention
Pipe routing: Adopt “top-supply/bottom-return” or “bottom-supply/bottom-return” layouts. Minimum slopes:
- 0.003 for metal pipes
- 0.01 for composite pipes
Support spacing: - ≤3m for DN25 steel pipes
- ≤1.5m for PP-R pipes
Use 3mm steel spacers between supports and pipes.
Welding specifications:
- Steel pipe crown welding with subsequent kerosene penetration testing
- Allow natural cooling for PP-R (5 minutes for DN25)
Pressure testing: - Cold systems: 0.6MPa for 30 min → max drop 0.02MPa
- Hot systems: 1.0MPa for 60 min → max drop 0.05MPa
Detailing: Eliminating Connection Leaks
Insulation requirements:
- Closed-cell rubber foam ≥20mm (for DN≤50 pipes)
- Apply specialty adhesive at joints
- Seal with aluminum foil tape
Install 50mm water seals at protective pipes. Branch-main connections: 45° angle. Terminate with tented caps. Critical components:
- Y-strainers (≥20 mesh) ≥5 pipe diameters from coil inlets
- Balancing valves on return lines
- Bronze ball valves at all coil connections
- Valves (≥DN20) at manifolds
- Manual air vents at system high points
Leak Repair & Maintenance: Long-Term Prevention
Leak diagnosis:
- Inspect PTFE tape application techniques
- Verify PP-R fusion bead formation (1-2mm)
Emergency repair: - Apply waterproof tape
- Install clamp-on rubber pads with stoppers
- Close upstream valves
Inspection protocols:
- Verify slopes with levels (±0.001 tolerance)
- Clean filter screens quarterly
- Annual hydrostatic retesting
- Replace flexible joints periodically
- Conduct condensate line tests using piping inspection balls (diameter ≥0.7 pipe diameter)
Implementing these material, installation, detailing, and maintenance procedures significantly reduces leakage risks. Translating them into operational protocols ensures long-term reliability of fan coil unit piping systems.